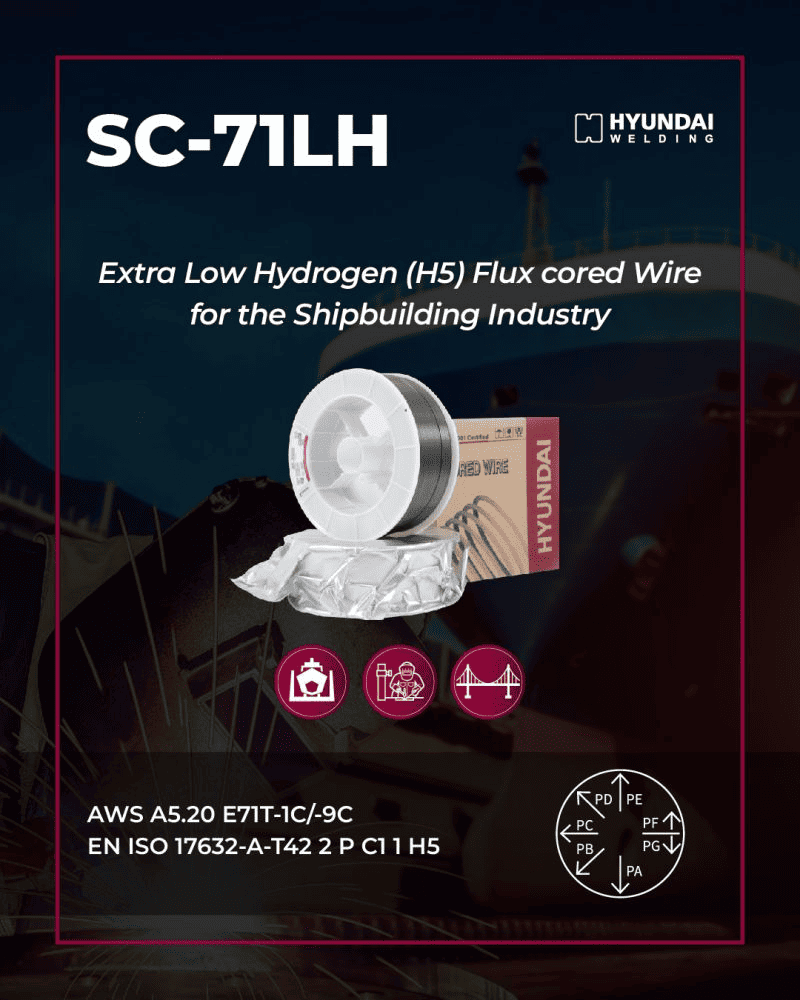
Maximizando la Eficiencia del Proceso GMAW: Consejos y Buenas Prácticas
El proceso GMAW (Gas Metal Arc Welding), también conocido como soldadura MIG/MAG, es ampliamente utilizado en la industria por su alta productividad, versatilidad y facilidad de automatización. Sin embargo, para garantizar soldaduras de alta calidad y evitar defectos, es fundamental seguir una serie de buenas prácticas en su aplicación.
A continuación, compartimos consejos clave para optimizar su uso y obtener uniones soldadas con excelente resistencia y acabado.
1. Selección del Gas de Protección Adecuado
El gas protector es esencial para evitar la contaminación y lograr una fusión uniforme del material base y el alambre. Las opciones más comunes son:
✔CO₂ puro: Ideal para aceros al carbono, ofrece buena penetración pero genera más salpicaduras.
✔Mezcla de argón y CO₂ (75%-25% o 80%-20%): Proporciona un arco más estable, menor salpicadura y mejor control del cordón.
✔Argón puro: Utilizado en soldadura de aluminio para un arco estable y uniones limpias.
✔Mezcla de argón con oxígeno o helio: Recomendado para aceros inoxidables y aplicaciones especializadas.
Tip: valide el flujo de gas adecuado consultando la ficha técnica que su proveedor le proporcione. Un flujo adecuado es vital para proteger adecuadamente a la soldadura (un exceso de flujo creará turbulencias en la salida del gas que
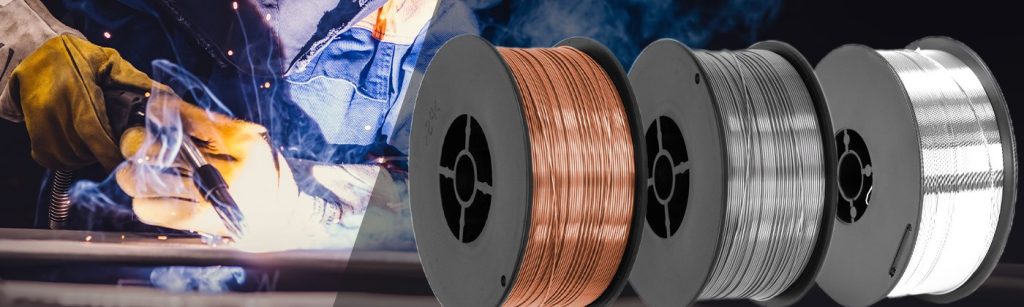
2.Elección del Alambre Correcto
El tipo de alambre es un factor clave en la calidad del proceso GMAW. Algunos de los micro alambres más populares según el material son:
✔Acero al carbono: ER70S-6 para máxima limpieza y buen desempeño en materiales con óxidos o impurezas.
✔Aceros inoxidables: ER308L para aceros inoxidables de composición similar (series: 201, 202, 301, 302, etc.) y ER309L para uniones tipo 304 y ocasionalmente aceros disimiles.
✔Aluminio: ER4043 o ER5356 dependiendo del contenido de magnesio en metal base.
Tip: Al elegir el diámetro del alambre es importante conocer la capacidad de el equipo que se esta utilizando y el espesor del metal base.
3.Ajuste de Parámetros de Soldadura
Para lograr una penetración uniforme y evitar defectos, es importante configurar correctamente:
✔Voltaje: Determina la longitud del arco y debe ajustarse según el grosor del material.
✔Velocidad de alimentación del alambre: Afecta la penetración y la estabilidad del arco.
✔Amperaje: Debe ser proporcional al diámetro del alambre y la velocidad de avance.
Tip: Mantenga una velocidad de desplazamiento constante al soldar y evite movimientos bruscos que puedan generar porosidad o falta de fusión.
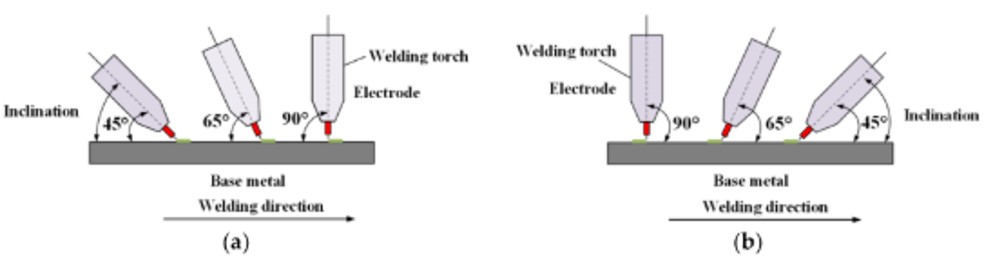
4.Posición y Técnica de Soldadura
Dependiendo de la posición de la junta, se recomienda:
✔Soldadura plana y horizontal: Use una técnica de empuje para lograr una mejor distribución del metal de aporte.
✔Posiciones verticales: Aplique una técnica de arrastre con menor voltaje para evitar el goteo del material fundido.
✔Posición sobre cabeza: Reduzca el amperaje y utilice un cordón en zigzag para mayor control del baño de fusión.
Tip: Mantenga una inclinación de la pistola de 10°-15° en la dirección de avance para un mejor control del charco de soldadura.
5.Mantenimiento y Cuidado del Equipo
Un equipo en óptimas condiciones garantiza soldaduras limpias y sin interrupciones. Para ello:
✔Revise periódicamente la punta de contacto, tobera y el difusor de gas para evitar obstrucciones.
✔Limpie el rodillo de alimentación y la guía del alambre para prevenir atascos.
✔Verifique la conexión de tierra para evitar arcos inestables o inconsistencias en la fusión.
Tip: Utilice anti salpicaduras cerámicas en su tobera esporádicamente para reducir la acumulación de salpicaduras y prolongar la vida útil de los consumibles.
Obtenga Resultados Óptimos con Soldaduras y Superaleaciones
Aplicar estas buenas prácticas en MIG/MAG mejorará la calidad, eficiencia y durabilidad de sus soldaduras. En Soldaduras y Superaleaciones, contamos con los alambres ideales para su aplicación, así como asesoría especializada para ayudarle a elegir los mejores insumos para su producción.